Casting from Organics
- Natalie
- Sep 7, 2015
- 7 min read
In every beginning casting class I’ve taken or taught, someone has asked the question “Can I use materials other than carved wax as my model?” Then answer is yes! You can use just about anything which burns as a model. Some pose more risks (plastics can emit harmful fumes), and some will burn out more thoroughly than others. I love casting from organics. The shapes and textures are something you just cannot achieve through carving (or even 3d modeling), but there are a number of challenges organic models present that wax does not. Casting from organics is not for those who NEED TO KNOW how it will turn out. Trial and error (and eventually success) is the way to go, so be flexible and forgiving when something doesn’t turn out perfectly the first time. Failures aren’t’ just failures, but a chance to troubleshoot and learn something new about casting.

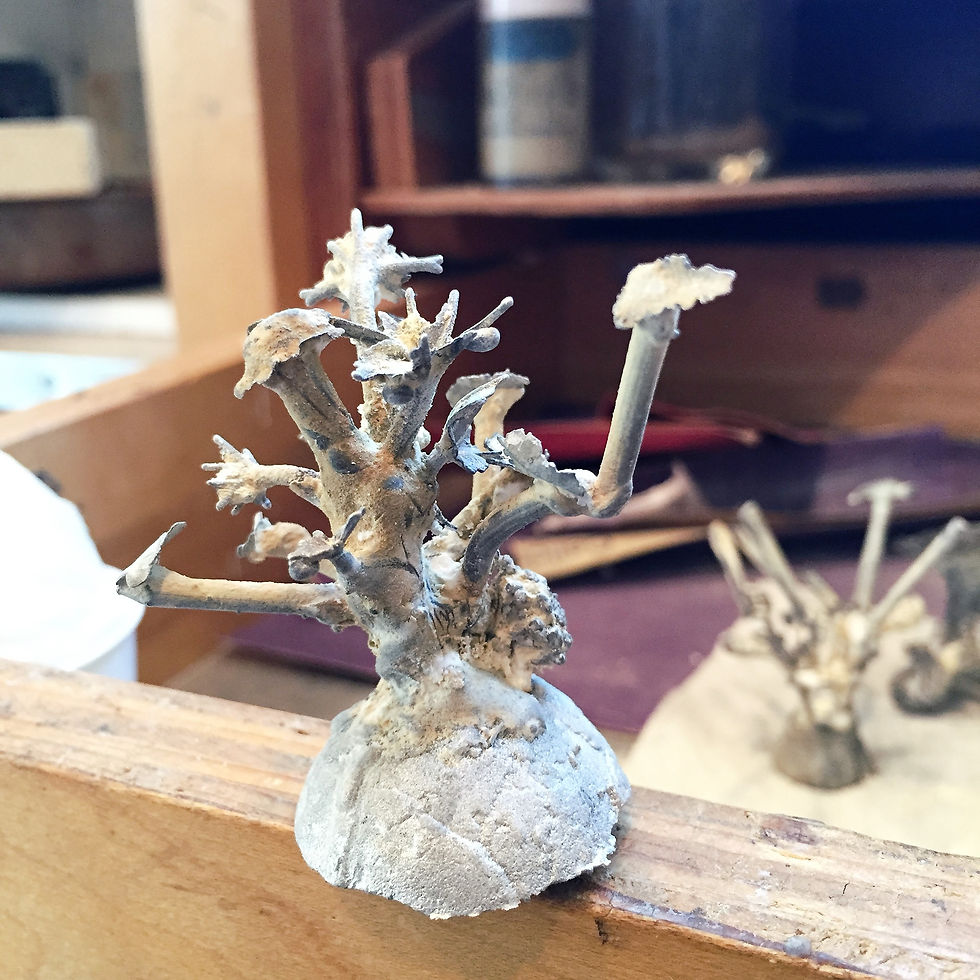

Choose your model: look for plants you would describe as leathery, and are on the thicker side. Most flowers do not fall into this category, since petals tend to be very thin (orchids are an exception, and I’m sure there are others as well). Succulents are my go-to category of organics, but even within that group, there are some which work better than others. Trial and error is often the only way to go. One of the harder aspects to keep in mind is the surface texture of the organic you’re using. Don’t forget that once you transform your plant into metal, it will lose its colors! Don’t be fooled by beautifully colored plants which lack any interesting shape or surface textures. Also, bear in mind how heavy your organic model will be once it’s converted into metal. You don’t want to end up with an anchor!
I have found the most success with green plants. Other materials, like wood, can also work, but may or may not burn out. Bone and bugs with exoskeletons typically don’t burn out, and I do not recommend them. Not sure if it will work? Try it! I’ve been surprised in both directions. Some plants seem like a sure thing, and just won’t work. Some look like a reach, and work beautifully. You won’t always know until you try.

Spruing: For the most part, spruing organic models is very similar to spruing wax models. You still want to aim for the thickest part of the piece, and to position your model in such a way as to allow the metal to fill easily (avoid forcing your metal to make U-turns, and don’t allow any portion to be lower than the button.) Remember to check for areas that will be difficult to fill: many plants get thinner towards the edges, so you may need to add a bead of wax along the edges to give your metal a little extra help. Sometimes additional sprues will be necessary to provide extra access to thin areas. The biggest challenge with spruing organics can be maintaining an even surface texture. Look for the smoothest areas, or spots which will be easily hidden in your final project.
Sticky wax is my absolute favorite wax for spruing. The typical blue or red wax most people use for wax models tends not to stick well to organic surfaces to begin with, and the very flexible nature of many plants can result in connections breaking, and much frustration as a result. The drawback is that sticky wax only comes in one (fairly large) gauge. My solution is to use a combination of sticky wax and blue wire wax of the appropriate size. I apply a small dab of sticky wax to my model in the spot I will place the sprue. Next, I add a dab of sticky wax to the end of the blue wax I will use as the sprue. While that’s still hot, push it firmly onto the prepped area of the model. The sticky wax should adhere fairly well. You can always add extra sticky wax to reinforce the connection, and use dental tools to smooth the joint out. Some plants have so much moisture in them the wax simply will not adhere well. For these cases, I will heat a flat dental tool and scorch the area where the sprue will be placed.
Just as with wax models, keep your sprues and connections as smooth as possible to prevent churning of the metal while casting, which can lead to porosity.

How much metal?: Another step to be completed prior to investing is determining how much metal you are going to need. Wax is easy- weigh your sprued piece and multiply by your metal’s specific gravity (silver is 10.6). Add 10 dwt for the button, and you’re all set! Unfortunately, organics don’t work this way. Water displacement* can be used, but I don’t find it particularly effective, as many plants will float on top of the water rather than sinking. Making a quick mock-up of your organic item with modeling wax is a great way to estimate how much metal you need, as it can be weighed as described above. After you have some experience casting, you will be able to eyeball how much metal you need. A helpful tip I picked up was using a little more metal than you might for a wax model. The extra weight can help push metal into thinner areas, but does carry some risks. Make sure you have sufficient room for a large button (choose a rubber base with a large bump). If you overshoot too much, you risk having so much metal in your button that the nose of the crucible sticks in the button, or excess metal escapes and is flung around the centrifuge. These are both huge issues, posing safety risks and potential damage to your equipment. Underestimating your metal needs is far less serious, but can result in not only an incomplete casting, but porosity as well. Estimating your metal will get easier with practice! Once you have a few pieces successfully cast, you can weigh them to get a better idea of how much metal each piece requires. Don’t forget to add enough metal to account for your sprues too!


Investing: Investing organics can pose a few additional challenges that wax models don’t. Very flexible plants can often shift while pouring your plaster, so go slowly! Pour your plaster into your flask like you would pour a beer: down the side, and slowly. I often rotate the flask slowly to help evenly distribute the investment, and occasionally fully upright the flask to allow the plants to resettle into their original spot. I have had the most success capturing better surface details by mixing my investment on the thin side (more water than usual). Don’t go overboard, but just an extra couple tablespoons of water can make a big difference.
Another tactic for avoiding bubbles, which can greatly disturb delicate surface details, is giving your model a quick dip in denatured alcohol just before pouring the investment into the flask. I will set aside a small cup of denatured alcohol before beginning to invest. While the investment is in the vacuum for the first round (while the plaster is in the mixing bowl), I pour the alcohol into my flask and give it a swirl around, making sure to coat my model. Pour out the alcohol, and pour in your investment. Ire-use the same alcohol for all flasks that day.
Burn Out: My best results have been achieved through a 7 hour burn out. My school (SMFA Boston) had a huge manual gas burnout kiln. Although you did need to be present to monitor the kiln’s temperature and make frequent adjustments, having that kind of control over the temperature was vital. I ramped up to 1250 over several hours, and soaked at 1250 for 2-3 hours. The kilns was then slowly reduced to 900. Currently, I’m casting at the Irvine Arts Center in Orange County, CA. The studio manager runs the burnouts, and they do not have a lot of people working in organics. Their burnout schedule is extremely short (only three hours) and the kiln is held at 1200 rather than 900 at the end of the cycle. It seems to do alright for wax, but it is not enough for most organics. I’ve pushed them to allow me to do slightly longer burnouts (5-6 hours), and have had moderate success at that length. However, my results have been spottier than with longer burnouts. If you are in control of your burn out, long and hot will help achieve your best results.
One effective tip for getting any ash out of your flask is gently tapping your flask (button side down) on a fireproof surface. I hold the flask at a 20 or so degree angle, and give a very light tap. Tilt the other way, and repeat. Just two or three taps can reduce any small ash piles which would otherwise affect your final piece.

Clean up: An ultrasonic, steam cleaner or sandblaster are all fantastic tools for cleaning up organic castings. Organics can have some really difficult to reach areas, so my preference is a combination of steam and ultrasonic. Sandblasters, as long as they are using very fine sand, can be very effective too, but they can also reduce the sharpness of your surface details. Many institutions also don’t allow sandblasting to clean castings, so make sure you’re allowed to use the machine for that purpose!
Check your finished pieces for areas which didn’t fill. These spots are caused by too thin of a model, or a poor burnout. Some areas may have cast well, but will need to be reinforced with solder: look for wiggly pieces with thin attachments.

What now?: One of the biggest challenges of casting organics is what to do with your pieces! Don’t forget that you are the metalsmith. You’re in charge of that piece, and you are not bound to keep it just as it came out of the flask. You can break pieces down, rearrange components and manipulate them in any way you choose. Make those casting work for you! If you find an element you love, you might want to make a rubber mold to be able to efficiently reproduce that item. RTV molds are a great option, and tend to capture complex forms effectively.
Porosity can be a big issue in all casting, but especially with organics. When you are ready to solder something to your cast element, I recommend burnishing that area prior to soldering. This can give you a stronger connection. If you notice that your cast element is sucking up all your solder, this is likely due to porosity. Consider having a greater amount to surface contact between the pieces you’re soldering to give more structural support.

*Water Displacement: Get a tall, skinny clear container. A graduated cylinder is ideal, but a tall thin drinking glass can work too. Fill the container half way with water, and put your model in the water. The water level will rise slightly. On the outside of the glass, mark the new water level. Remove your piece (try not to remove any water with it!). Start adding your casting metal to the container until the water level reaches the mark you made. This works regardless of what metal you’re using because you are measuring volume, not weight. This is not the most accurate way of measuring, but is effective when no other method is available.
Comments